High Volume Component Cost Optimization
Comprehensive Power Conversion Solutions for Every Need
Your Trusted Development Partner.
Strategic Cost Optimization
Reducing component costs at scale requires a strategic approach that balances performance, quality, and affordability. By analyzing high-volume production requirements, we implement cost-saving measures such as material substitutions, process efficiencies, and supplier negotiations to drive down expenses while maintaining product integrity.
Efficient Supply Chain Management
A well-structured supply chain minimizes risks and reduces procurement costs. We work closely with trusted manufacturers and distributors to ensure steady component availability, reduce lead times, and negotiate volume discounts. Our dynamic sourcing strategies help mitigate price fluctuations and potential shortages.
Scalability and Cost Reduction Strategies
As demand scales, cost structures evolve. We implement modular design strategies that allow for cost-effective upgrades and adaptations. Our solutions include designing for manufacturability (DFM), minimizing part count, and reducing assembly complexity to drive down long-term production costs. Additionally, we explore advanced fabrication techniques such as injection molding and die-casting for high-volume efficiency.
Optimized Component Selection
Choosing the right components impacts both cost and performance. We conduct a thorough analysis of alternatives, ensuring that selected components meet technical specifications without unnecessary overhead. Our approach includes evaluating alternative suppliers, leveraging bulk pricing advantages, and selecting standardized parts to avoid custom fabrication costs.
Manufacturing Process Optimization
Streamlining production processes is key to reducing waste and increasing efficiency. We identify automation opportunities, optimize assembly workflows, and refine manufacturing techniques to lower production costs. By implementing lean manufacturing principles, we enhance throughput without compromising quality.

I Want To…..
Opt for non-isolated designs that simplify power conversion and reduce energy losses. These solutions are compact and cost-effective, making them suitable for systems where space and budget constraints are priorities.
Employ circuits with efficient heat dissipation mechanisms. Both isolated and non-isolated solutions are engineered for stable, long-term operation, even in high-load or high-temperature environments.
Utilize adaptable designs that fit seamlessly into a wide range of applications. Our circuits are compatible with both industrial systems and consumer devices, ensuring broad usability and convenience.
Select non-isolated designs for cost-sensitive projects without sacrificing performance. Simplified architectures minimize material and production expenses while delivering reliable power conversion.
Choose isolated designs with galvanic isolation to protect sensitive components and users. These circuits are ideal for applications requiring high reliability and adherence to stringent safety standards.
Optimization is an ongoing process. We establish robust cost-monitoring systems that track component pricing trends, assess supplier performance, and identify new opportunities for cost savings. Through periodic evaluations and data-driven insights, we ensure sustained cost efficiency in high-volume production environments.
I Want To…..
Opt for non-isolated designs that simplify power conversion and reduce energy losses. These solutions are compact and cost-effective, making them suitable for systems where space and budget constraints are priorities.
Employ circuits with efficient heat dissipation mechanisms. Both isolated and non-isolated solutions are engineered for stable, long-term operation, even in high-load or high-temperature environments.
Utilize adaptable designs that fit seamlessly into a wide range of applications. Our circuits are compatible with both industrial systems and consumer devices, ensuring broad usability and convenience.
Select non-isolated designs for cost-sensitive projects without sacrificing performance. Simplified architectures minimize material and production expenses while delivering reliable power conversion.
Choose isolated designs with galvanic isolation to protect sensitive components and users. These circuits are ideal for applications requiring high reliability and adherence to stringent safety standards.
Optimization is an ongoing process. We establish robust cost-monitoring systems that track component pricing trends, assess supplier performance, and identify new opportunities for cost savings. Through periodic evaluations and data-driven insights, we ensure sustained cost efficiency in high-volume production environments.
Application-Specific Design
Generic, one-size-fits-all component solutions rarely deliver optimal cost-effectiveness in high-volume applications. Our design philosophy begins with a deep dive into understanding the specific nuances of your product and its intended use environment. We analyze factors such as operating temperatures, power requirements, performance targets, expected lifespan, and regulatory compliance. This granular understanding enables us to tailor component selection and design from the ground up, ensuring that every component serves a specific purpose and contributes to the overall value proposition of the product.
Intelligent Material Selection
The choice of materials plays a crucial role in both the performance and cost of a component. We go beyond simply selecting the cheapest available material. Our team of materials scientists and engineers carefully evaluates a wide range of materials, considering factors like cost, availability, durability, performance characteristics (e.g., conductivity, strength, thermal properties), and environmental impact. We explore innovative materials and manufacturing processes, such as advanced polymers, composites, and additive manufacturing, to identify cost-effective alternatives to traditional materials.
Comprehensive Component Analysis and Optimization
We conduct thorough teardown analyses and cost modeling of existing products or proposed designs to identify opportunities for component cost reduction. This includes evaluating component specifications, identifying potential substitutes with comparable performance but lower cost, and exploring different package types or form factors. We also analyze the supply chain for each component, looking for opportunities to consolidate suppliers, leverage volume discounts, or negotiate better pricing.
Strategic Supplier Partnerships
Strong relationships with trusted suppliers are essential for securing competitive pricing and ensuring a reliable supply of high-quality components. We cultivate long-term partnerships with key suppliers, leveraging our collective buying power to negotiate favorable terms and volume discounts. We also work closely with suppliers to identify opportunities for joint cost reduction initiatives, such as optimizing component design or improving manufacturing processes.
Value Engineering and Value Analysis
We employ value engineering and value analysis methodologies to systematically examine every aspect of the product, from its functionality to its cost. The goal is to identify and eliminate any unnecessary costs without compromising the product’s value or performance. This involves a collaborative process that brings together engineers, designers, manufacturing specialists, and marketing professionals to challenge assumptions and explore alternative solutions.
Lean Manufacturing Principles
We implement lean manufacturing principles throughout our production facilities to eliminate waste, improve efficiency, and reduce costs. This includes techniques such as just-in-time inventory management, kanban systems, and continuous flow manufacturing.
Automation and Robotics
We leverage automation and robotics to streamline manufacturing processes, reduce labor costs, and improve product consistency. Automated assembly lines, robotic handling systems, and automated testing equipment are strategically deployed to maximize efficiency and minimize human error.
Process Optimization and Continuous Improvement
We continuously monitor and analyze our manufacturing processes to identify areas for improvement. We use statistical process control and other quality management tools to track key metrics and identify opportunities to reduce defects, improve yields, and optimize production flow.
Smart Prototyping and Simulation
We utilize advanced prototyping techniques, including 3D printing, rapid tooling, and simulation software, to quickly and cost-effectively validate designs and identify potential issues early in the development cycle. This reduces the need for costly physical prototypes and minimizes the risk of design errors that could lead to expensive rework later in the production process.
Design Verification and Testing
Rigorous design verification and testing are essential to ensure that components and products meet all performance and quality requirements. We develop comprehensive test plans that cover all critical parameters and utilize automated test equipment whenever possible to reduce testing time and costs.
Global Sourcing Strategies
We explore global sourcing opportunities to identify suppliers who can offer the best combination of price, quality, and lead times. We carefully evaluate potential suppliers based on their capabilities, reliability, and financial stability.
Inventory Management
We implement sophisticated inventory management systems to optimize inventory levels, minimize carrying costs, and prevent stockouts. We use demand forecasting and other analytical tools to predict future demand and adjust inventory levels accordingly.
Have a question or need expert advice? Contact us now, and let’s bring your ideas to life!
Solutions
Material Selection for Cost Efficiency
The choice of materials directly impacts cost and performance. We analyze the application requirements and select cost-effective alternatives without compromising reliability. For example, replacing rare-earth metals with high-performance composites or using polymer-based substrates instead of traditional metals can significantly reduce expenses.
Design for Manufacturability (DFM)
DFM principles streamline production by optimizing component geometry, reducing part count, and simplifying assembly. By incorporating standardized dimensions, snap-fit designs, and modularity, we minimize waste and improve manufacturability, leading to significant cost savings in large-scale production.
Automation and Lean Manufacturing
Automated assembly lines, robotic precision manufacturing, and AI-driven quality control significantly reduce labor costs and enhance production efficiency. By integrating Industry 4.0 solutions, such as predictive maintenance and real-time monitoring, we ensure minimal downtime and optimal resource utilization.
Supplier Negotiation and Bulk Procurement
Establishing long-term partnerships with reliable suppliers allows for volume-based discounts and favorable contract terms. Through strategic negotiations and global sourcing, we secure high-quality components at competitive prices while reducing lead times.
Alternative Sourcing Strategies
Diversifying supplier networks and leveraging second-source suppliers mitigate risks associated with supply chain disruptions. We analyze multiple vendors and explore cost-effective procurement options, ensuring uninterrupted production flow while reducing dependency on a single supplier.
Logistics and Inventory Management
Optimizing inventory management through just-in-time (JIT) strategies and demand forecasting minimizes excess stock while preventing shortages. Advanced tracking systems enable real-time inventory visibility, ensuring efficient warehouse operations and reduced carrying costs.
Advanced Fabrication Techniques
Utilizing high-precision molding, laser cutting, and automated soldering reduces production errors and scrap rates. Techniques such as 3D printing for prototyping accelerate development cycles while keeping initial tooling costs low.
Component Standardization and Modular Design
Standardizing components across multiple product lines simplifies procurement and enables bulk purchasing advantages. Modular design principles allow for easy interchangeability, reducing the need for custom components and lowering overall production costs.
Integrated Testing and Defect Prevention
Implementing automated testing and real-time quality analysis prevents costly rework and product recalls. By ensuring compliance with industry standards and utilizing Six Sigma methodologies, we maintain high-quality output while minimizing waste and defective units.
Lifecycle Cost Analysis
Beyond initial production, we assess the total cost of ownership (TCO) to optimize long-term savings. This includes factors such as energy consumption, maintenance costs, and end-of-life recyclability, ensuring sustainable and cost-effective solutions.
Eco-Friendly Manufacturing Practices
Incorporating sustainable materials, energy-efficient production methods, and waste reduction strategies contribute to cost savings and regulatory compliance. We implement closed-loop recycling systems and eco-friendly packaging to minimize environmental impact while optimizing production efficiency.
Renewable Energy Utilization
Adopting solar, wind, and other renewable energy sources in manufacturing facilities helps reduce dependency on fossil fuels, lowering operational costs and carbon footprint. By integrating energy-efficient machinery and smart grid technologies, we further optimize energy consumption.
Sustainable Material Sourcing
Utilizing biodegradable plastics, recycled metals, and responsibly sourced raw materials ensures environmental responsibility while maintaining product quality. Partnering with certified green suppliers strengthens sustainability efforts and aligns with regulatory requirements.
Waste Management and Recycling
Developing comprehensive waste management programs, including material reclamation and industrial recycling initiatives, minimizes landfill contributions and promotes circular economy principles. Implementing on-site recycling facilities further enhances sustainability.
Material Selection for Cost Efficiency
The choice of materials directly impacts cost and performance. We analyze the application requirements and select cost-effective alternatives without compromising reliability. For example, replacing rare-earth metals with high-performance composites or using polymer-based substrates instead of traditional metals can significantly reduce expenses.
Design for Manufacturability (DFM)
DFM principles streamline production by optimizing component geometry, reducing part count, and simplifying assembly. By incorporating standardized dimensions, snap-fit designs, and modularity, we minimize waste and improve manufacturability, leading to significant cost savings in large-scale production.
Automation and Lean Manufacturing
Automated assembly lines, robotic precision manufacturing, and AI-driven quality control significantly reduce labor costs and enhance production efficiency. By integrating Industry 4.0 solutions, such as predictive maintenance and real-time monitoring, we ensure minimal downtime and optimal resource utilization.
Supplier Negotiation and Bulk Procurement
Establishing long-term partnerships with reliable suppliers allows for volume-based discounts and favorable contract terms. Through strategic negotiations and global sourcing, we secure high-quality components at competitive prices while reducing lead times.
Alternative Sourcing Strategies
Diversifying supplier networks and leveraging second-source suppliers mitigate risks associated with supply chain disruptions. We analyze multiple vendors and explore cost-effective procurement options, ensuring uninterrupted production flow while reducing dependency on a single supplier.
Logistics and Inventory Management
Optimizing inventory management through just-in-time (JIT) strategies and demand forecasting minimizes excess stock while preventing shortages. Advanced tracking systems enable real-time inventory visibility, ensuring efficient warehouse operations and reduced carrying costs.
Advanced Fabrication Techniques
Utilizing high-precision molding, laser cutting, and automated soldering reduces production errors and scrap rates. Techniques such as 3D printing for prototyping accelerate development cycles while keeping initial tooling costs low.
Component Standardization and Modular Design
Standardizing components across multiple product lines simplifies procurement and enables bulk purchasing advantages. Modular design principles allow for easy interchangeability, reducing the need for custom components and lowering overall production costs.
Integrated Testing and Defect Prevention
Implementing automated testing and real-time quality analysis prevents costly rework and product recalls. By ensuring compliance with industry standards and utilizing Six Sigma methodologies, we maintain high-quality output while minimizing waste and defective units.
Lifecycle Cost Analysis
Beyond initial production, we assess the total cost of ownership (TCO) to optimize long-term savings. This includes factors such as energy consumption, maintenance costs, and end-of-life recyclability, ensuring sustainable and cost-effective solutions.
Eco-Friendly Manufacturing Practices
Incorporating sustainable materials, energy-efficient production methods, and waste reduction strategies contribute to cost savings and regulatory compliance. We implement closed-loop recycling systems and eco-friendly packaging to minimize environmental impact while optimizing production efficiency.
Renewable Energy Utilization
Adopting solar, wind, and other renewable energy sources in manufacturing facilities helps reduce dependency on fossil fuels, lowering operational costs and carbon footprint. By integrating energy-efficient machinery and smart grid technologies, we further optimize energy consumption.
Sustainable Material Sourcing
Utilizing biodegradable plastics, recycled metals, and responsibly sourced raw materials ensures environmental responsibility while maintaining product quality. Partnering with certified green suppliers strengthens sustainability efforts and aligns with regulatory requirements.
Waste Management and Recycling
Developing comprehensive waste management programs, including material reclamation and industrial recycling initiatives, minimizes landfill contributions and promotes circular economy principles. Implementing on-site recycling facilities further enhances sustainability.
Specialist Services
High Efficiency
Achieve maximum cost-effectiveness via minimized resource consumption. Our development process focuses on energy-efficient designs and optimized material usage, reducing waste and lowering per-unit costs for high-volume applications.
Compact Designs
Minimize component size and footprint to reduce material costs and enable integration into smaller, more cost-effective devices. Our expertise in miniaturization allows us to develop compact components without sacrificing performance.
Cost Optimization
Reduce production costs and improve efficiency through optimized manufacturing processes tailored for high-volume production. We consider automation, tooling, assembly, and testability to minimize expenses and maximize throughput.
Streamlined Manufacturing
Reduce production costs and improve efficiency through optimized manufacturing processes tailored for high-volume production. We consider automation, tooling, assembly, and testability to minimize expenses and maximize throughput.
Scalable Development
Our development process is designed for scalability, quickly and efficiently adapting to changing requirements and high production volumes. We utilize modular designs and flexible manufacturing to ensure components can easily scale.
Performance Optimization
Maximize component performance while minimizing cost. We carefully balance performance requirements with cost considerations, ensuring components meet specifications without unnecessary features or over-engineered solutions.
High Efficiency
Achieve maximum cost-effectiveness via minimized resource consumption. Our development process focuses on energy-efficient designs and optimized material usage, reducing waste and lowering per-unit costs for high-volume applications.
Compact Designs
Minimize component size and footprint to reduce material costs and enable integration into smaller, more cost-devices. Our expertise in miniaturization allows us to develop compact components without sacrificing performance.
Cost Optimization
Combine affordability with high performance. Through streamlined manufacturing, optimized material selection, and strategic supplier partnerships, our development process caters to cost-sensitive, high-volume applications.
Streamlined Manufacturing
Reduce production costs and improve efficiency through optimized manufacturing processes tailored for high-volume production. We consider automation, tooling, assembly, and testability to minimize expenses and maximize throughput.
Performance Optimization
Maximize component performance while minimizing cost. We carefully balance performance requirements with cost considerations, ensuring components meet specifications without unnecessary features or over-engineered solutions.
Scalable Development
Our development process is designed for scalability, quickly and efficiently adapting to changing requirements and high production volumes. We utilize modular designs and flexible manufacturing to ensure components can easily scale.
Development
Next-Generation Material Integration
Utilizing composite materials, advanced polymers, and alternative alloys can significantly reduce costs while maintaining performance standards. By replacing traditional components with high-strength, lightweight alternatives, manufacturers can decrease production expenses and improve product longevity.
Sustainable Material Sourcing
Investing in recyclable and renewable materials helps balance cost savings with environmental responsibility. Strategies such as reusing industrial byproducts and sourcing from certified sustainable suppliers reduce waste and ensure compliance with global regulations.
Material Performance Enhancement
Advanced coatings, nanotechnology applications, and material reinforcement techniques improve the durability and lifespan of components. These innovations enable manufacturers to reduce failure rates, lower maintenance costs, and enhance overall product reliability.
Smart Automation Implementation
Deploying AI-driven automation in assembly lines enhances production efficiency and lowers labor costs. Machine learning algorithms can predict maintenance needs, preventing downtime and maximizing operational throughput.
Lean Manufacturing Principles
Eliminating redundant processes and optimizing production flow can significantly improve cost efficiency. Techniques such as Six Sigma and just-in-time (JIT) inventory management help reduce waste and ensure a streamlined workflow.
Real-Time Process Monitoring
Implementing IoT-based sensors and cloud analytics enables real-time tracking of manufacturing processes. This ensures rapid detection of inefficiencies, allowing for immediate corrective actions to reduce waste and enhance productivity.
Data-Driven Procurement Strategies
Using predictive analytics, manufacturers can optimize bulk purchasing and supplier negotiations, ensuring cost-effective sourcing of raw materials while maintaining supply stability.
Decentralized Supply Chain Models
Establishing multiple supply chain hubs reduces dependency on single-source suppliers and minimizes transportation costs. This approach also enhances flexibility in response to market fluctuations and supply disruptions.
Supplier Collaboration and Transparency
Developing strong supplier relationships and leveraging blockchain technology for transparent transactions improves trust, reduces lead times, and enhances overall supply chain efficiency.
Modular Component Design
Designing components with modular adaptability allows manufacturers to leverage economies of scale while offering product customization. This reduces production complexity and enables quicker adaptations to market trends.
Rapid Prototyping and Agile Development
Implementing 3D printing and digital twin simulations accelerates product development cycles. This reduces material waste during prototype testing and minimizes costly design errors in mass production.
Flexible Manufacturing Systems
Adopting reconfigurable production lines and adaptive robotics allows for seamless transitions between product variations. This enhances scalability while ensuring rapid response to evolving market demands.
Renewable Energy Utilization
Manufacturing facilities can cut energy expenses by integrating solar, wind, and hydroelectric power. Investing in energy-efficient machinery and grid-responsive technologies enhances sustainability while lowering operational costs.
Renewable Energy Utilization
Adopting solar, wind, and other renewable energy sources in manufacturing facilities helps reduce dependency on fossil fuels, lowering operational costs and carbon footprint. By integrating energy-efficient machinery and smart grid technologies, we further optimize energy consumption.
Carbon Footprint Reduction Initiatives
Implementing carbon capture technologies, optimizing logistics for reduced emissions, and adopting greener transportation methods contribute to a lower environmental impact while improving regulatory compliance.
Next-Generation Material Integration
Utilizing composite materials, advanced polymers, and alternative alloys can significantly reduce costs while maintaining performance standards. By replacing traditional components with high-strength, lightweight alternatives, manufacturers can decrease production expenses and improve product longevity.
Sustainable Material Sourcing
Investing in recyclable and renewable materials helps balance cost savings with environmental responsibility. Strategies such as reusing industrial byproducts and sourcing from certified sustainable suppliers reduce waste and ensure compliance with global regulations.
Material Performance Enhancement
Advanced coatings, nanotechnology applications, and material reinforcement techniques improve the durability and lifespan of components. These innovations enable manufacturers to reduce failure rates, lower maintenance costs, and enhance overall product reliability.
Smart Automation Implementation
Deploying AI-driven automation in assembly lines enhances production efficiency and lowers labor costs. Machine learning algorithms can predict maintenance needs, preventing downtime and maximizing operational throughput.
Lean Manufacturing Principles
Eliminating redundant processes and optimizing production flow can significantly improve cost efficiency. Techniques such as Six Sigma and just-in-time (JIT) inventory management help reduce waste and ensure a streamlined workflow.
Real-Time Process Monitoring
Implementing IoT-based sensors and cloud analytics enables real-time tracking of manufacturing processes. This ensures rapid detection of inefficiencies, allowing for immediate corrective actions to reduce waste and enhance productivity.
Data-Driven Procurement Strategies
Using predictive analytics, manufacturers can optimize bulk purchasing and supplier negotiations, ensuring cost-effective sourcing of raw materials while maintaining supply stability.
Decentralized Supply Chain Models
Establishing multiple supply chain hubs reduces dependency on single-source suppliers and minimizes transportation costs. This approach also enhances flexibility in response to market fluctuations and supply disruptions.
Supplier Collaboration and Transparency
Developing strong supplier relationships and leveraging blockchain technology for transparent transactions improves trust, reduces lead times, and enhances overall supply chain efficiency.
Modular Component Design
Designing components with modular adaptability allows manufacturers to leverage economies of scale while offering product customization. This reduces production complexity and enables quicker adaptations to market trends.
Rapid Prototyping and Agile Development
Implementing 3D printing and digital twin simulations accelerates product development cycles. This reduces material waste during prototype testing and minimizes costly design errors in mass production.
Flexible Manufacturing Systems
Adopting reconfigurable production lines and adaptive robotics allows for seamless transitions between product variations. This enhances scalability while ensuring rapid response to evolving market demands.
Renewable Energy Utilization
Manufacturing facilities can cut energy expenses by integrating solar, wind, and hydroelectric power. Investing in energy-efficient machinery and grid-responsive technologies enhances sustainability while lowering operational costs.
Renewable Energy Utilization
Adopting solar, wind, and other renewable energy sources in manufacturing facilities helps reduce dependency on fossil fuels, lowering operational costs and carbon footprint. By integrating energy-efficient machinery and smart grid technologies, we further optimize energy consumption.
Carbon Footprint Reduction Initiatives
Implementing carbon capture technologies, optimizing logistics for reduced emissions, and adopting greener transportation methods contribute to a lower environmental impact while improving regulatory compliance.
Contact Us Today
Latest news
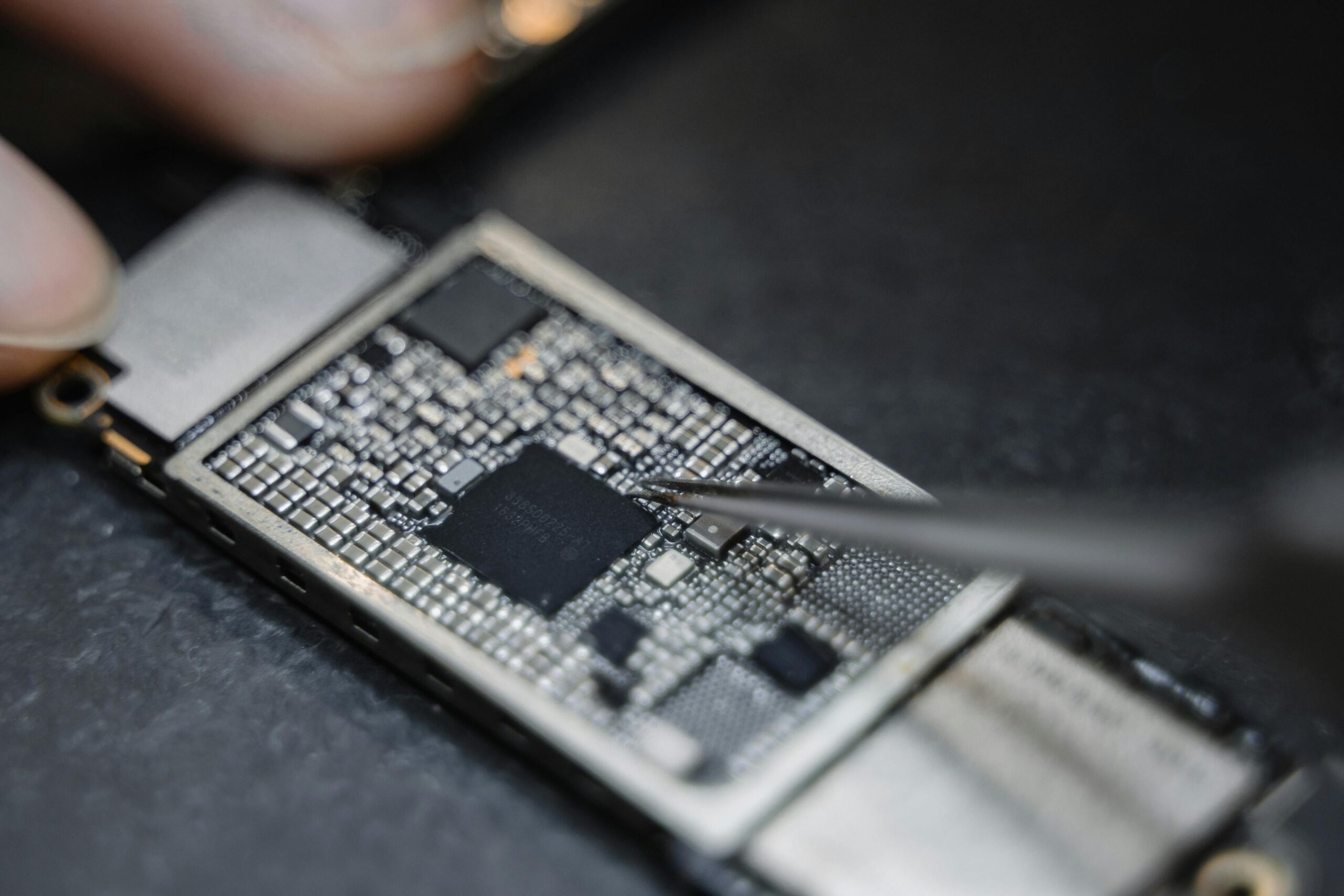
Achieving Excellence with Skilled Engineering Contractors
In today’s rapidly evolving technology landscape, businesses often face a critical question: How do we[…]
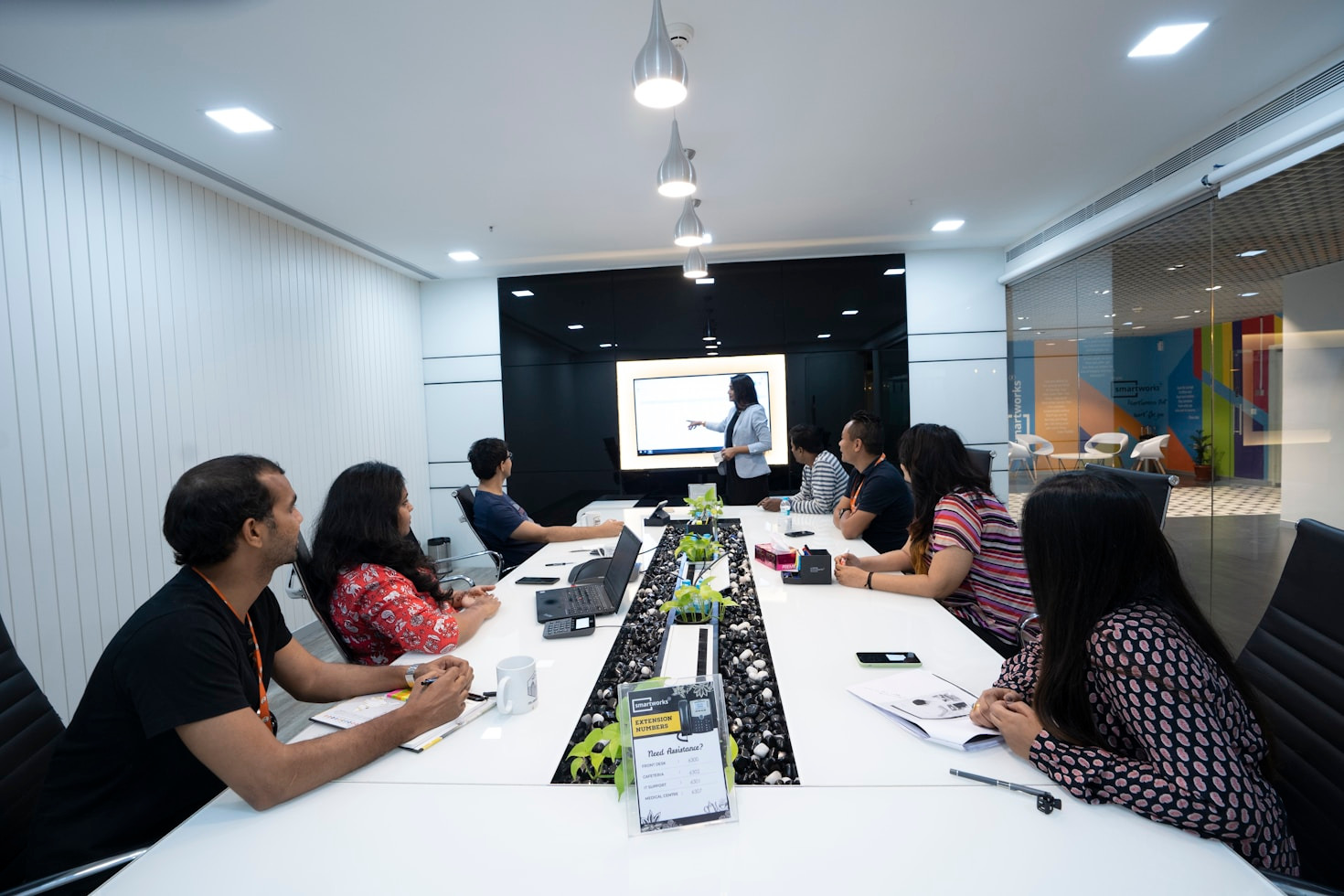
Innovative Engineering Solutions for Modern Challenges
Today’s world moves fast — and it’s only accelerating. From AI-driven devices to sustainable infrastructure[…]
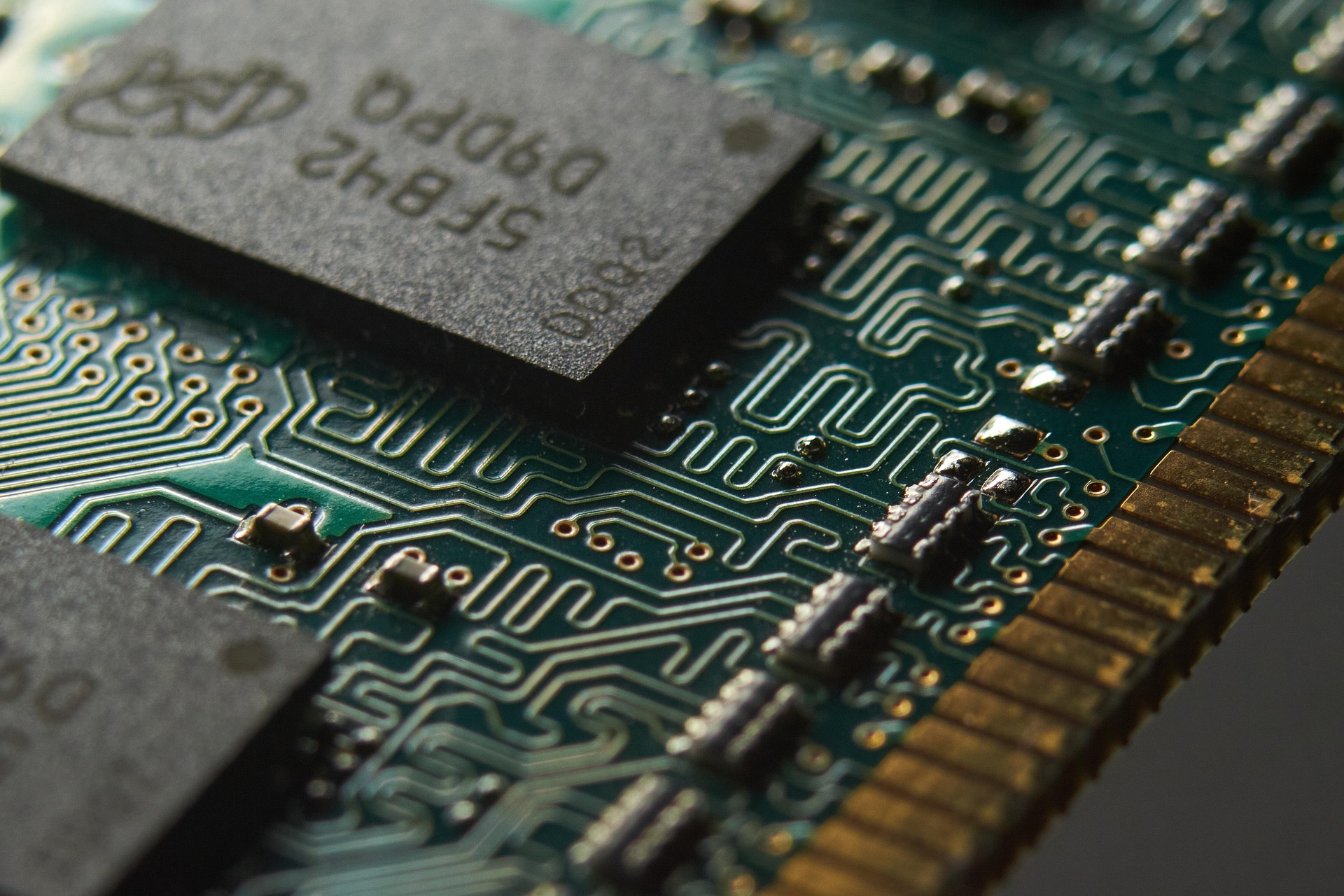
Why Experience Matters in Engineering Services
In the world of engineering, precision isn’t a luxury — it’s a requirement. Whether it’s[…]